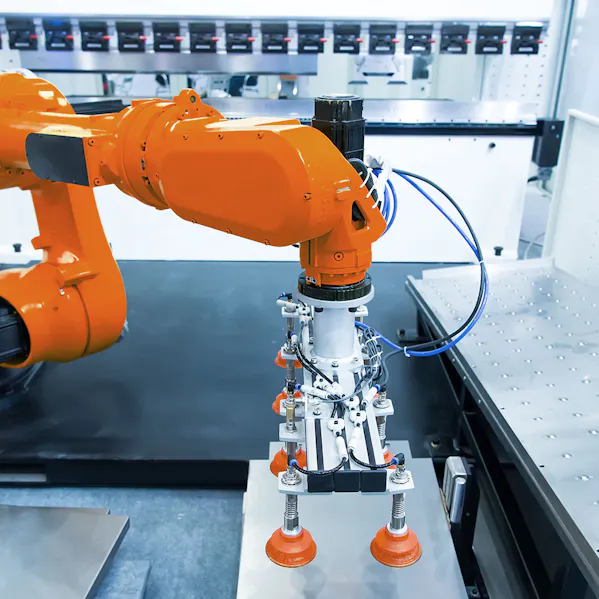
IMPLEMENTING INDUSTRIAL IOT SCENARIOS
ENTRY-LEVEL IOT
Interconnectedness is on the rise; so, too, the number of communication touch points. This is true for both people and machines. The growth of the Industrial Internet of Things is driven in particular by increased availability of data, and growing affordability and higher performance of technology (especially sensors).
IoT and Industry 4.0 are not solely defined by technology and innovative IT scenarios. As we see it, the methods used to identify beneficial use cases cannot be separated from the IoT context. This includes design thinking for defining and evaluating problems and for creating appropriate solution scenarios as well as agile methods to implement IoT projects.
IOT FIELDS OF ACTION
Specific IoT fields of action can be found in machine integration, the collection, storage and preparation of data related to particular use cases and the integration of this data into systems and applications. Naturally, our focus here is on the SAP ERP and its mapped business processes. In turn, these processes can be improved using the additional information collected. Often, innovative approaches lead to completely new business models.
Connecting machines to the world of IT and its networks is the prerequisite for all IoT scenarios. At the same time, the connection itself can often be a challenge, for example in heterogeneous machine facilities or older facilities. In any case, connecting machines requires a look at OPC UA, Edge, big data and machine learning, among others.
OUR APPROACH
Aside from the wide world of technological aspects and challenges, the business must be integrated right from the start for the IoT project to be able to get off the ground. This in turns allows the specific cost benefit of a project to be determined. If, however, the business context is not considered sufficiently, a project can be quickly lost in unstructured data collection efforts.
Considering cost benefits is also simply a sensible thing to do and thus important. This is because Industry 4.0 is a new, innovative area in which experience has yet to be obtained. Ultimately, experience can be gained only through implementation. To prevent the obstacles from being too steep for getting started, we rely on standards as the basis for the implementation of individual scenarios and solutions appropriate for your context. Generally applicable, usable standards are available in SAP solutions SAP Leonardo, SAP AIN), cloud platforms (SAP Cloud Platform, Microsoft Azure) or the OPC UA industry standard for integrating machine data.
IOT SCENARIOS ARE GENERALLY CHARACTERISED BY A STEEP LEARNING CURVE. AS A RESULT, TAKING INITIATIVE ALWAYS PAYS OFF.
CONCRETE USE CASES
Condition monitoring is a basic use case for IoT, involving real-time monitoring of the conditions of machines and facilities. Under condition monitoring, shutdowns and downtimes can be reduced, for example, and data aggregated. Solutions based on this data can be implemented using machine learning and predictive maintenance. Predictive maintenance increases machine availability for operators and allows mechanical engineers to offer new services.
Both mechanical engineers and machine operators tend to view data exchange from different perspectives: while operators often focus on integrating into the production process different machines, typically from a variety of manufacturers, manufacturers typically focus on communication with the machines within their scope.
This aspect is mirrored in the concept of digital twins. A digital twin is a virtual map of a real object, such as a machine, allowing it to be interconnected with another object, both real and virtual. This opens entirely new business opportunities for manufacturers as operating devices, services, marketing and the roles of manufacturers and customers changes as a result. In the SAP environment, the Asset Intelligence Network (AIN) is the basis of the digital twin. This merges information from manufacturers, service providers and facilities operators on a cloud-based platform.
Real-time data exchange is the foundation of the Smart Factory concept for which we offer an SAP-orientated solution suitable for roll-outs: interconnected, intelligent production and vertical integration of machine data permit the optimisation of existing service and production workflows.
The integration of ERP and machine data is likewise the basis of pay-per-use scenarios or implementing lot size 1. Under pay-per-use, manufacturers are no longer selling machines as such, but the output of the machines. And this is what is allowing for new business models. When orders are passed on fully automatically to intelligent production, individualised customer orders down to lot size 1 can also be implemented more economically.
GETTING STARTED WITH IOT
An IoT project is not created from within a vacuum. It must fit precisely in your context to ensure its success and that the added value is indeed delivered. Our approach is to work up a specific use case with you and define either a project or proof of concept based on the use case. To arrive at this point and coordinate this with all stakeholders at your company, we have developed a comprehensive offering of workshops.